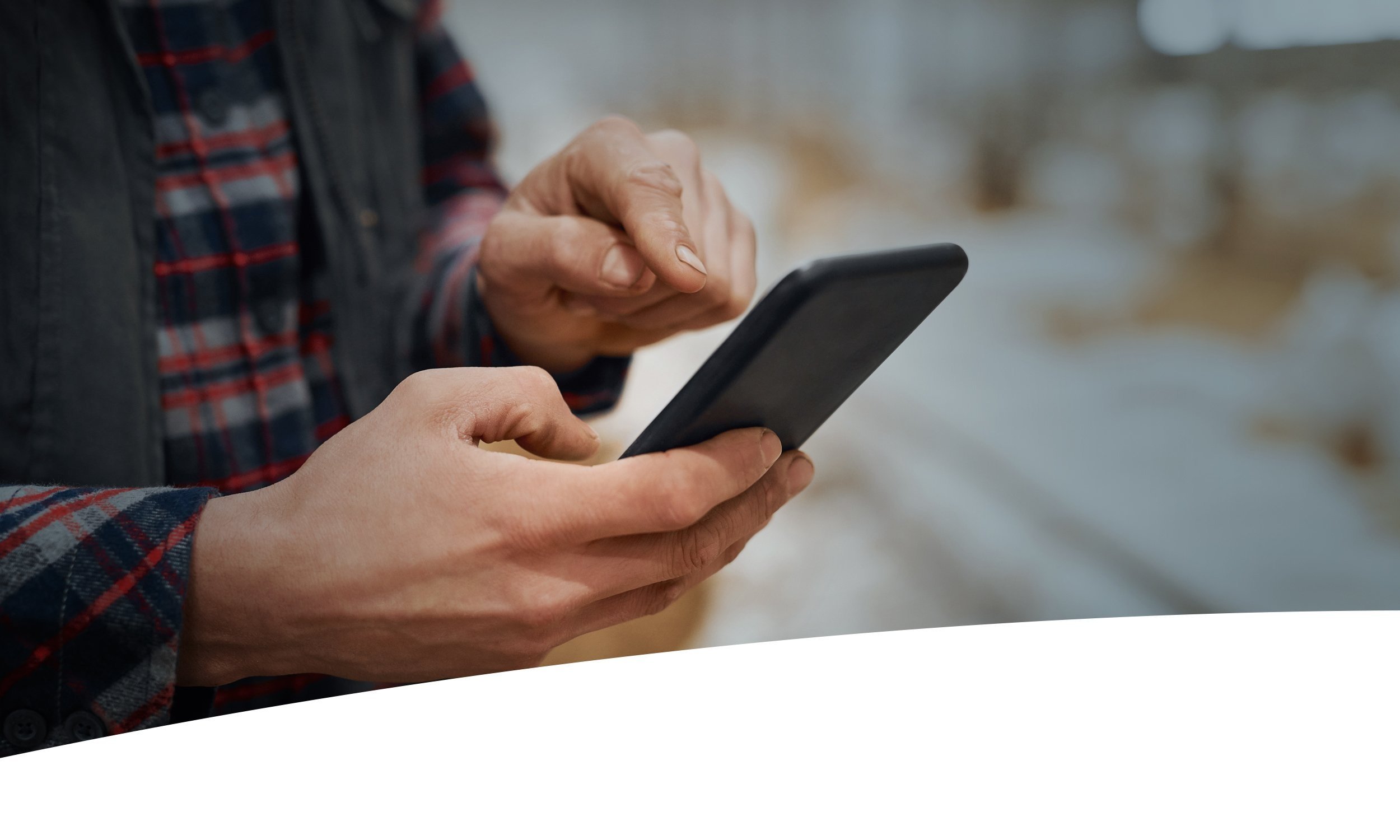
FAQs
See below for a list of frequently asked questions
General
-
Whilst silos are by far the best solution for biosecure feed storage they often pose a challenge to accurately calculate how much feed is in the silo for reordering purposes, so whilst it looks like there is plenty of feed in the silo it can be deceiving and easy to misjudge, the result . . . runouts and over orders and both can be costly.
Silo monitoring changes all this and gives the insight needed for better feed management, its low-cost too, often costing less than the impact an outage would have on your yield loss!
Order from the FeedAlert team, it’s a self-installation to keep the cost down but don’t worry its quick and easy, perhaps taking up to 30 minutes on your first install and then after set-up you’re up and running. View data on the App or local display and outages should become a thing of the past. Less hassle, time saving, maintain FCR or yield and relive the stress of feed management, FeedAlert is low-cost to ensure maximum industry take up as the more people that have the system, the greater the benefit to the Feed manufacturers and ultimately this intelligence will allow them to become more efficient and prices should reflect this. So everyone benefits, changing agriculture for the better.
-
Smart farming, also known as smart agriculture or precision agriculture involves using IoT based hardware technology, sending data to the cloud for viewing remotely, the additional intelligence in the form of data is then used, by smart farmers 😉, to better manage their farming activities, increasing productivity and efficiency, and of course ultimately profits!
A Smart Silo falls into this category, the IoT technology and sensors create a tool that sits under the Smart farming umbrella, providing valuable information for better feed/silo management.
Preventing feed outages and over orders make all farmers, not just smart but happy too!
For enhanced industry management farmers can choose to give shared visibility of data to their feed supplier, this intelligence enable the supplier to offer an enhanced feed management service but it also provides them a tool to optimise operations to unlock environmental and financial savings.
Basically silo monitoring is a win, win for the whole industry!
-
There is a silo monitoring system for all silos, whether you want low cost inventory control, you want to utilise existing load cells or you need precision monitoring for data analysis, get in touch for a chat and we’ll adv se on the right system for you.
-
Yes, yes, yes . . . any make of silo with a metal support structure, which if not all, is most silos. Silos with round leg structures do require a leg fixing bracket, these are available in 4 sizes; 90mm, 102mm, 114mm, 140mm and are specified to suit the leg diameter.
-
Our initial R&D didn’t include skirted silos however we have a number of customers using FeedAlert on their skirted silos with success, we say, give it a go.
-
It’s a low-cost silo monitoring solution, systems start from £450 + vat, the basic app is free, here you can track the weight in the silo and see days to run out.
-
FeedAlert installation is quick and easy, it takes less than 30 minutes if you follow the step by step instructions in the installation guidance, you can also watch the video.
-
No, the basic app is absolutely free!
-
No, there is no cost for an end user to view the silo data on the App. Once the silo monitoring hardware is installed on the silo there are no ongoing subscription costs.
-
Telephone the FeedAlert team on 01995 606451 and choose option 5. We need to know the customer trading name and contact details together with the silo make (if you know) and capacity.
Online ordering will be available soon.
New Users
-
Its simple, get the silo empty then zero it.
Fill the silo, the heavier the better, we recommend more than 50% of capacity on the first fill.
Calibrate the silo to the delivered amount, prior to using any feed. This zero/calibrate action sets the weighing scale for the silo.
Use the feed and enjoy the benefits of the data.
Best Practise: Zero and calibrate the silo if it becomes empty, it is recommended to zero and calibrate a couple of times a year, a good reminder is when the clocks change.
-
Yes, ideally. If it isn’t empty you’re guessing at how much is in the silo and so post setup the data is reliant on that guess, if it is empty, the data is based on exactly what is in the silo.
So, you stand the best chance of optimum accuracy if the silo Is empty prior to setting up. Although IF it is not possible to get the silo empty, it is possible to get the silo as empty as possible, then guesstimate how much is in the silo prior to zeroing, this can then be added, mentally, when assessing silo levels. Whilst this is a good indicator, it is obviously susceptible to miscalculation and should not be wholly relied on.
Existing Users
-
Best Practise: Zero and calibrate the silo if it becomes empty, it is recommended to zero and calibrate a couple of times a year as the temperature changes, a good reminder is when the clocks change.
If you are happy with the weights then leave the system to do its thing, if the variant is at the top end of the vairiant window grab the opportunity to zero and reset when it is empty.
-
The system is typically able to achieve 95% accuracy of full capacity on a four leg silo. The Installation & Guidance booklet does include tips on how best to achieve optimum performance.
For systems with more than four legs a second sensor can be added to maintain the accuracy window.
-
It is possible to achieve reliable readings with FeedAlert. If you’re not achieving 95% accuracy, get in touch with the team and we will dig into the data and see if there are any anomalies.
The Installation & Guidance booklet does include tips on how best to achieve optimum performance.
-
Absolutely, yes and whats more it is easy to control in the App. Choose the menu, select Silo Sharing you will then be presented with all your silos, select the silo you would like to share and follow the instructions.
If you don't have the App, phone the team on 01995 606451 and choose option 5, let us know who you would like to share your silo with and we'll sort it for you.
more eyes on the silo the better. Currently it’s a manual share, just let us know and we’ll make it happen. Shortly this will be possible via the App.
Sharing visibility with your feed supplier will enable them to provide enhanced customer support and informed order/delivery decisions can be agreed.
Visibility of the data also enables suppliers to optimise operations with more effective production runs and logistics planning for an improved environmental footprint.
-
It is possible to use FeedAlert in bad signal areas, yes.
Dependent upon the signal strength different levels of access can be achieved.
The SIM is 4G enabled but can drop back to 2G for data transfer, the system only sends small amounts of data so whereas you would need full signal strength for a phone call, the data can utilise 2G, achieving coverage for a large amount of the UK.
IF 2G is not available on a site, a customer can have a Capture system and whilst the data will not be available for remote viewing, users can use the local display to manage feed with confidence.
-
There is a ten year warranty on the sensor and a 1 year warranty on the control, both commence from invoice date.
If your system has a fault, get in touch with the team for diagnosis.
If a system needs replacing, we will dispatch a replacement system and arrange for the old system to be collected, minimising downtime.
-
Go into the mobile App, select the silo you wish to change the name of. Once in the silo record open the menu, top right, and select Silo Summary. Add the new name to ‘New silo name and save the changes.
If you have multiple sites / silos a handy tip is to include the site name in the silo name eg. Brow Farm_Silo1 this can easily be located in an alphabetical list.
-
Accuracy is wholly dependent upon the quality of the data added on set-up however this can be updated at any time to refine accuracy.
Using the volume of the manufacturers specification provides a more accurate starting point than just knowing it is a eg. 12 tonne silo however the latter is better than nothing!
To edit the capacity of your silo, enter the silo record on your app, select the menu – top right, and choose Silo summary. In here you can edit the silo name and cubic capacity of the silo.
-
It is good practice to ensure the correct product is recorded as being in the silo as the density can affect the data.
If you are sharing data with your supplier they will update your record, if you are managing your silo yourself, to update a product stored record, enter the silo record, select Product. Choose the correct product, if you are sharing your data with your supplier choose the brand name. If you aren’t sharing, select one of the standard default feed types.
-
Get in touch to add team members, we will need a name, mobile number and email and we'll get an invite sent to them.
This feature will be coming to the App shortly.
-
Capacity and fill level is calculated using the silo volume and the density of the product being stored. We have default densities for each feed type, ensuring the correct product type is registered in the silo provides the best accuracy.
If you share data with your feed supplier, they can add your bespoke product as being stored, this increases the accuracy on the data provided.
The capacity of the silo is calculated using the volume of the silo
-
As with any weighing instruments, FeedAlert should be calibrated regularly to assure they are measuring correctly.
Once a good accuracy has been achieved from initial set-up you can use the silo on a regular basis and it will continue to show the weight.
It is recommended to repeat set-up with a zero/calibration to realign the weight a couple of times a year, clock changing is a good time.
Also repeat calibration if the system needs aligning or if there is a product change.
-
To receive weight data and alerts via the app the system needs to be plugged in.
If for any reason you do need to unplug it, don’t worry, if the system has been set-up and a calibrated scale set, when powered back up it will use this scale to reset the weight.
This also covers lightening strikes or power outages, once power returns to the unit it will automatically take a weight reading and continue as normal.
-
Default alert levels are set at, low - 30% and very low – 10% of the silo capacity.
-
Notification settings are individual to the user and each team member can manage their own preferences.
You can choose if you receive notifications by email and/or push notifications. Individual alerts; low, very low, empty, over capacity can be set in each silo.
-
Low level notifications are intended to let you know that an order needs to be place and so we advise that these are maintained if you are managing a silo however ultimately it is the users choice.
You can manage which type of notifications you receive in the main menu - global notifications select between Push notifications and/or Email notifications. Individual silo notifications are managed in the individual silo menu , low, very low, empty and over capacity, simply turn them on and off as required.
-
Yes you can! Not only can you utilise existing load cells, if your existing load cells go into a BMS or house monitoring system, the cells can be upgraded to provide the information FeedAlert too, get in touch to find out how.
-
Nope, if it has been successfully calibrated before the power cut it will automatically weigh the contents and update the weight.
Note, on a strain gauge system if this happens during the day and heat and sunlight may distort that particular reading, don’t worry though this will realign at your evening weigh.
-
No FeedAlert isn’t a ‘Trade approved’ weighing device. For a weighing device to be classed as trade approved it must be passed as fit for use by a weights and measures inspector or approved verifier.
-
If you sell your silo you can choose i you sell FeedAlert with it or remove it and put it on a different silo. Either way, just get in touch with the team on 01995 606451, option 5, and let them know the new owner/site details.
To get up and running just repeat the system set-up. Details can be found at Inventory Control Installation Guidance.
-
Take the system off the old silo and put it to good use on another silo, whether you put it on your new silo or give/sell it to someone with a silo.
-
Absolutely, yes!
We prioritise the security of data above all else. As the leading UK Silo monitoring company, we implement robust encryption protocols to ensure that your data is protected during both transmission and storage. Our encryption methods adhere to the highest industry standards, safeguarding your information against unauthorised access and cyber threats.
We are fully compliant with the General Data Protection Regulation (GDPR), demonstrating our commitment to protecting the privacy and integrity of your personal data. By adhering to GDPR, we ensure that your data is processed lawfully, fairly, and transparently.
Trouble Shooting
-
There are different considerations, or techniques which contribute to the accuracy of FeedAlert, for tips on how to achieve optimum accuracy see page 3 in the installation guidance booklet Inventory Control Installation Guidance.
-
The days to runout is based on the previous 7/14/28 days data, dependent upon your chosen view, if your silo is inactive for during this period this will affect the forecasting but don’t worry, as data is collected this will become available again.
-
In the first instance, have you authorised notifications during onboarding, if not you can update this preference in your phone settings >notifications - just check that they are set to on for FeedAlert.
If they are and you're still not getting the notifications check your settings in the FeedAlert App to ensure notifications have not been turned off, if they have simply slide the button to on.
If the settings are on and you're still not getting notified, contact the FeedAlert team on 01995 606451, choose option 5, who will investigate the glitch.
-
Oops, but don’t worry!
If you have zeroed your silo AFTER feed has been blown in get in touch with the team, IF a successful zero has been done before this action we can dig into the data and potentially correct the error.
-
If the display is totally blank check the power is turned on.
-
If you have a strain gauge solution the weight updates once daily ~23:30, although if there is a power loss the system will automatically take a new reading.
If the app and display don’t tally, refresh the app screen by pulling down, this updates the data and the figures should then tally.
For load cell systems, data on the app is updated at 23:30 and also following a fill or discharge of >1000kg. Live app data for load cell systems is coming soon.
-
Strain gauge technology is subject to different variants, heat, sun etc and so the reading is taken once daily at ~23:30 to ensure consistent data at a time that daylight/heat isn’t distorting the reading.
Days to runout is calculated using your average daily usage.
If you have any queries about the data get in touch with the team on 01995 606451 and choose option 5, they will check the data and advise the best solution.
Data gives the team many different insights that aren’t immediately visible on the app, so it is always worth a call for advice on how to best refine the accuracy.
-
All new systems will be added to the app, if you can’t see your silo then get in touch with the team on 01995 606 451, choose option 5.

Still have a question
we haven’t covered?
We’d love to hear from you if you have any more questions for us
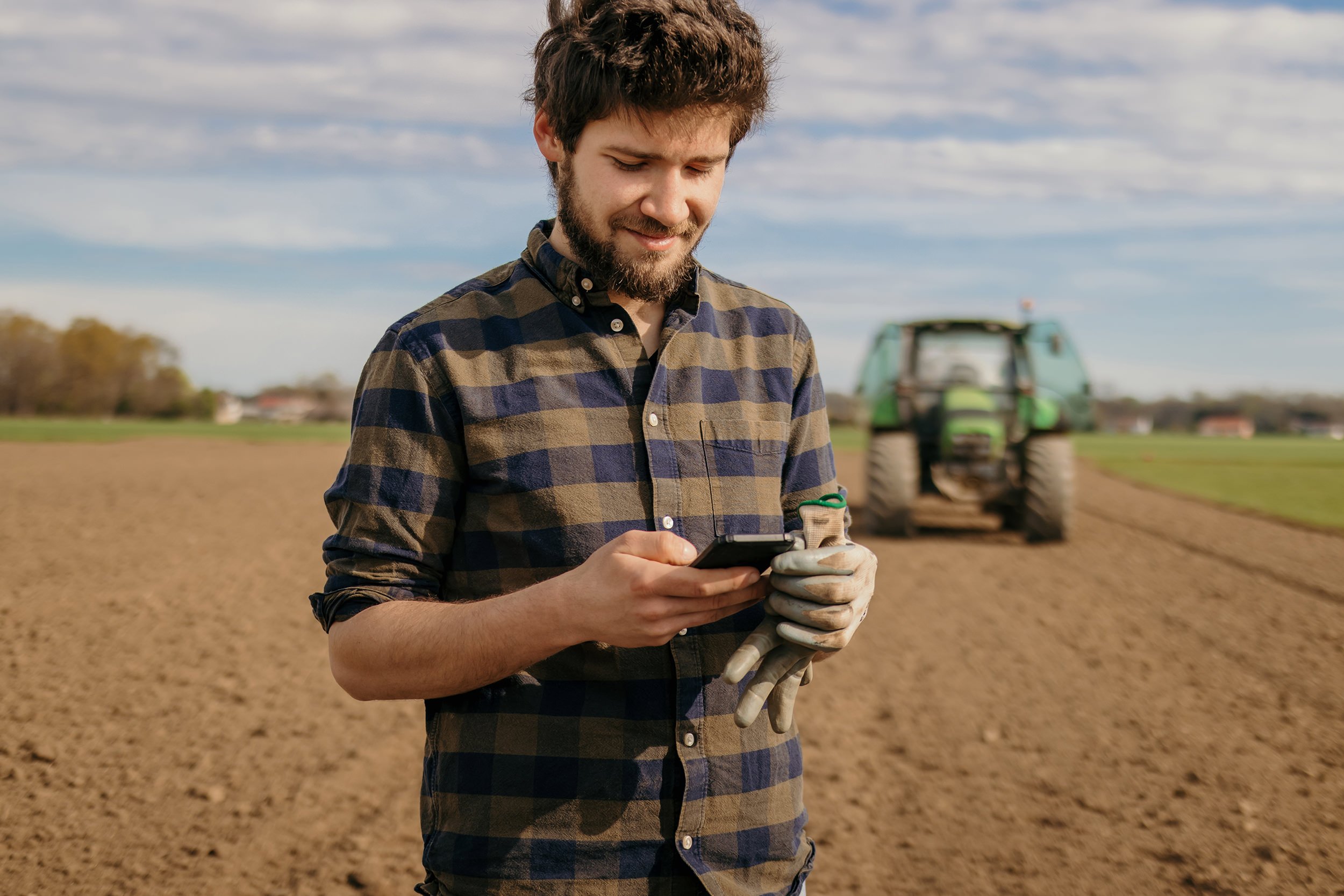
#MySmartSilo
Follow us on social media to keep up to date with our news and events. We want to hear from you too, we love seeing our silos and equipment in action, so if you take a photo, post it and tag us!